In the fast-evolving landscape of industrial automation and motor development, precision isn’t just a goal—it’s a necessity. Whether you’re designing cutting-edge electric vehicles, optimizing industrial machinery, or pushing the boundaries of renewable energy systems, the reliability of your motor testing equipment determines success. Enter hysteresis technology—a game-changer in braking, dynamometry, and clutch systems that delivers unmatched accuracy, durability, and adaptability.
🌐 **The Science Behind Hysteresis: Where Innovation Meets Performance**
Hysteresis brakes, dynamometers, and clutches leverage the unique magnetic properties of materials to create non-contact torque control. Unlike traditional friction-based systems, hysteresis devices eliminate wear and tear, ensuring consistent performance over thousands of cycles. This technology relies on the magnetic hysteresis loss principle, where energy dissipation occurs as magnetic domains realign, providing smooth, vibration-free torque modulation.
For motor test systems, this translates to repeatable results, reduced maintenance costs, and the ability to simulate real-world conditions with lifelike precision. Imagine testing an EV motor’s efficiency under varying loads or validating a drone propeller’s durability—all without physical contact interfering with measurements.
🔥 **Hysteresis Brakes: The Silent Guardians of Precision**
Hysteresis brakes are the unsung heroes in applications demanding silent operation and minimal maintenance. From textile machinery requiring tension control to aerospace actuators needing fail-safe braking, these devices excel where noise and particulate contamination are unacceptable.
Case in point: A leading robotics manufacturer integrated hysteresis brakes into their collaborative robots’ joints. The result? Smoother motion profiles, zero audible disturbance in sterile healthcare environments, and a 40% reduction in downtime caused by brake replacements.
🎯 **Hysteresis Dynamometers: Capturing Data, Unleashing Potential**
Modern motor testing demands more than just torque measurement—it requires dynamic adaptability. Hysteresis dynamometers shine here, offering instant load adjustments for testing motors under abrupt speed changes or fluctuating power inputs.
Take the example of an e-bike motor developer. By using a hysteresis-based dynamometer, they replicated uphill climbs, sudden stops, and regenerative braking scenarios with millisecond-level response times. The outcome? A 15% improvement in battery efficiency and a product that outperformed competitors in real-world endurance trials.
🔄 **Hysteresis Clutches: Seamless Power Transfer, Zero Compromise**
In applications where slip control is critical—think packaging lines or precision servo systems—hysteresis clutches provide torque limiting without mechanical wear. Their ability to maintain consistent slip torque regardless of rotational speed makes them ideal for overload protection and tension regulation.
A food processing plant grappling with conveyor belt slippage adopted hysteresis clutches to manage variable package weights. Modular automation systems eliminated product damage but also reduced energy waste by 22% through optimized power distribution.
🚀 **Motor Test Systems: Building Tomorrow’s Technology Today**
A comprehensive motor test system integrates hysteresis components with IoT-enabled analytics, creating a feedback loop that accelerates R\u0026D cycles. Real-time data on efficiency, thermal behavior, and harmonic distortion empowers engineers to iterate faster and innovate smarter.
Consider the challenge faced by a wind turbine manufacturer. By deploying a motor test system with hysteresis dynamometers, they simulated decades of operational stress in weeks, identifying insulation weaknesses in generator coils before production. This proactive approach slashed warranty claims by 34% and cemented their reputation for reliability.
💡 **Why Hysteresis Outshines Traditional Alternatives**
1. **Longevity**: No physical contact means no wear. Hysteresis devices often outlast their mechanical counterparts by 3x.
2. **Precision**: Sub-1% torque accuracy ensures compliance with stringent industry standards like ISO 17025.
3. **Versatility**: From micro-motors in medical devices to 10,000 HP industrial engines, hysteresis systems scale effortlessly.
4. **Sustainability**: Reduced energy consumption and elimination of lubricants align with ESG goals.
🔧 **Customization: Tailoring Solutions for Unique Challenges**
Off-the-shelf solutions rarely fit niche applications. Leading providers now offer modular hysteresis systems, allowing users to mix and control multiple brakes/dynamometers in a single setup. A drone propulsion lab, for instance, combined a 5 Nm hysteresis brake with a high-speed dynamometer to test quadcopter motors under gust simulation—an impossible feat with conventional rigs.
📈 **The ROI of Smart Testing Infrastructure**
Investing in advanced motor test equipment isn’t an expense—it’s a strategic advantage. Early adopters report:
- 50% faster time-to-market for new motor designs.
- 30% lower warranty costs due to pre-emptive failure detection.
- 20% energy savings through optimized motor efficiency profiles.
A European auto OEM shared that upgrading to hysteresis-based test benches cut their EV powertrain validation costs by €2.3 million annually, paying back the investment in under 18 months.
🌍 **Driving the Future: Hysteresis in Emerging Technologies**
As industries pivot toward electrification and AI-driven automation, hysteresis technology is evolving to meet new demands. Innovations like:
- **Hybrid Hysteresis-Eddy Current Systems**: Combining instant torque control with high-power dissipation for EV regenerative braking tests.
- **AI-Powered Predictive Models**: Using dynamometer data to forecast motor lifespan under extreme conditions.
- **Miniaturized Hysteresis Modules**: Enabling wafer-thin clutches for wearable robotics and micro-UAVs.
🔬 **The Lab-to-Factory Floor Continuum**
From prototype validation to production line QC, hysteresis-based systems bridge the gap between R\u0026D and manufacturing. A case study from a HVAC compressor producer highlights this: By standardizing test protocols across labs and factories using identical hysteresis dynamometers, they achieved a 90% correlation between lab results and field performance—up from 65% with previous systems.
🤝 **Partnering for Success: Choosing the Right Provider**
Selecting a hysteresis solution provider requires evaluating:
- **Application Expertise**: Do they understand your industry’s pain points?
- **Calibration Certifications**: Look for NIST-traceable or DAkkS-accredited systems.
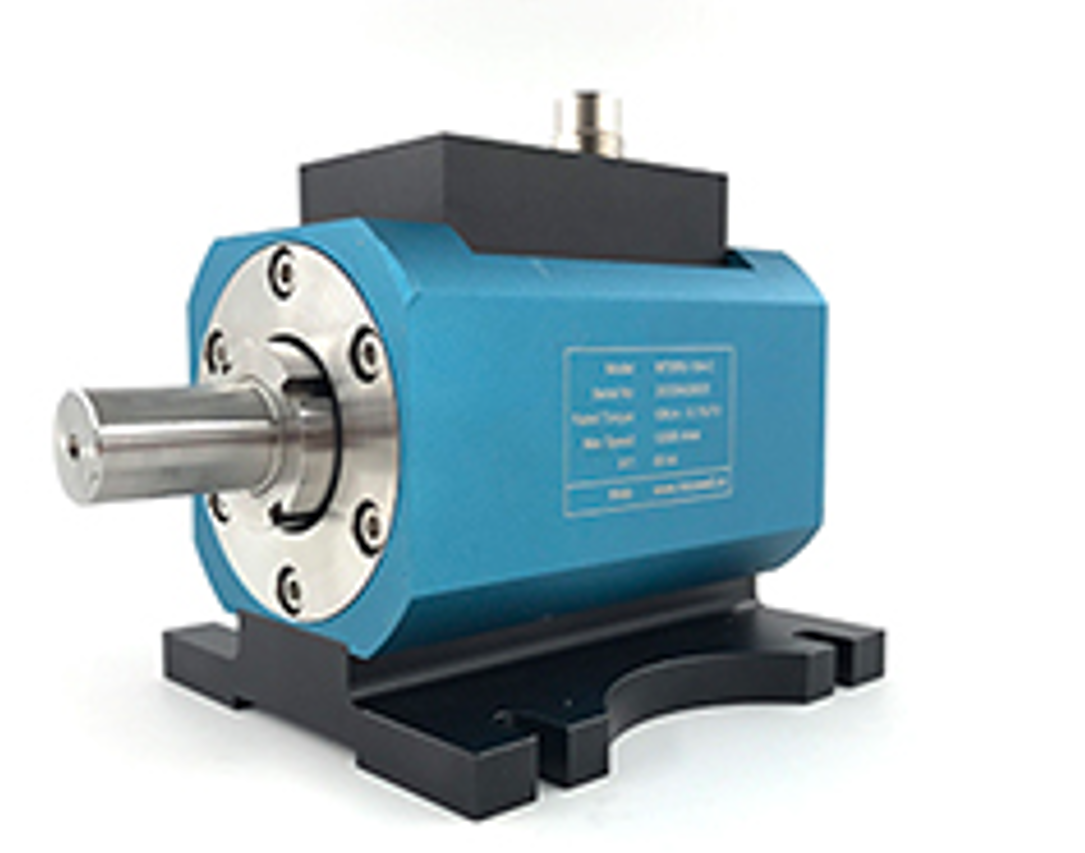
- **Software Integration**: Can their controllers interface with your existing MATLAB, LabVIEW, or Python workflows?
- **Global Support**: Rapid technical assistance minimizes downtime.
A solar pump manufacturer learned this the hard way after a supplier’s slow response delayed a product launch. Switching to a provider with 24/7 support and regional service hubs saved 200+ engineering hours yearly.
📢 **Final Thought: Precision Isn’t Optional—It’s Existential**
In a world where motor efficiency differences of 0.5% determine market leadership, settling for outdated testing methods is a gamble few can afford. Hysteresis technology isn’t just about measuring torque—it’s about unlocking possibilities, building trust in your products, and shaping industries.
The question isn’t whether you can integrate these systems. It’s how quickly you can start.